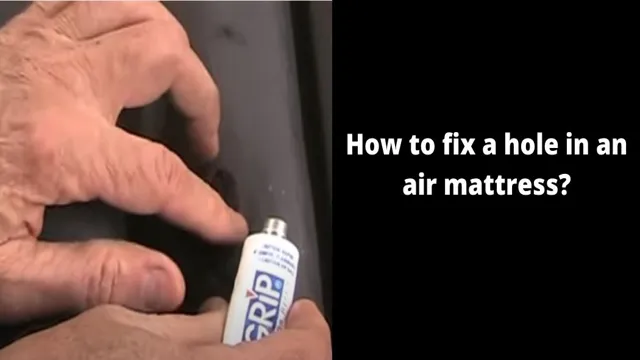
Have you ever been in the middle of a DIY project or working on your car when suddenly you hear a loud hissing sound coming from your air compressor? You quickly realize that a hole has formed in the hose, and now you’re in a bit of a bind. Don’t worry, though; repairing a hole in an air compressor hose is actually easier than you might think. Firstly, you’ll need to locate the hole.
This may be easier said than done, especially if the hole is small or hard to see. Try feeling around the hose with your hands or listening for the hissing sound to help identify the location. Once you’ve found the hole, cut out the affected section of the hose using a sharp utility knife.
It’s important to cut straight across the hose to ensure a clean, even cut. Next, you’ll need to purchase a hose repair kit from your local hardware store. This kit typically includes a barbed fitting and two hose clamps.
Slide the barbed fitting into the end of the hose and secure it in place with the hose clamps. Be sure to tighten the clamps securely to prevent any air leaks. Finally, turn on your air compressor and check for any leaks.
If you notice any hissing sounds or feel any air escaping, tighten the clamps further until the leak stops. In conclusion, fixing a hole in an air compressor hose is a fairly simple process that can be done with a few tools and a little bit of know-how. With this guide, you’ll be able to quickly and easily get your air compressor up and running again in no time.
Identify the Location of the Hole
If you’re dealing with a hole in your air compressor hose, the first step is to identify where the hole is located. Begin by examining the length of the hose for any visible damage, such as cuts or punctures. If you can’t see any evidence of damage, try turning on the compressor and feeling for air leaks along the length of the hose.
Another method is to submerge sections of the hose in water while it’s under pressure. The presence of bubbles will indicate where the hole is located. Once you’ve found the hole, mark it with a Sharpie or a piece of tape so you can easily locate it later.
Remember to turn off the compressor and release any pressure from the hose before attempting any repairs. With a bit of patience and determination, fixing a hole in an air compressor hose is a simple and cost-effective task that can be done with basic tools and materials.
Listen for hissing sound or feel for air escaping
When you suspect that you have a hole in your tire, the first thing to do is to investigate where it could be located. To begin with, you need to follow these simple steps to identify the location of the hole. First, inflate the tire using a pump and listen for any hissing sounds, or feel for escaping air, to determine the location of the hole.
Once you have done this, you can also try submerging the tire into a bucket of water, or using a sponge with soapy water to identify where the bubbles are coming from, revealing the hole’s location. If you are not able to find the specific location of the hole, then it is best to take the tire to a specialist to avoid any further complications. Once you have identified the location of the hole, you can decide whether to patch or replace the tire.
By doing this, you can prevent any accidents on the road, and you could save yourself time and money in the long run. So, be vigilant and pay attention to your tires, and keep them in good condition to avoid any issues in the future.
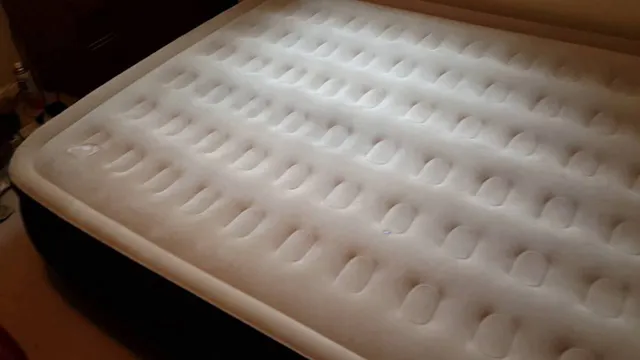
Inspect the hose visually
When inspecting a hose for holes or damage, it’s crucial to visually identify the location of the issue. Take a close look at the entire length of the hose, searching for any signs of wear, discoloration, or visible holes. Start at one end of the hose and work your way down slowly, giving each section adequate attention.
When you come across any abnormalities, take note of the location and size of the issue. Once you’ve covered the entire hose, you can go back and examine the problematic areas more closely. Locating the hole in the hose is the first step in repairing it.
It’s important to find the hole’s exact position to ensure that your repair efforts are effective, and the hose works properly. You don’t want to waste time and resources fixing the wrong spot. By identifying the location of the hole, you can make a more precise repair that will last longer and be more efficient.
By taking the time to inspect the hose carefully, you can catch any issues early and prevent further damage from occurring. Regular maintenance checks can help prolong the life of your hoses and prevent unexpected failures.
Turn Off the Compressor and Release Pressure
If you find a hole in your air compressor hose, don’t panic! It’s a common problem that can be easily fixed. The first step is to turn off the compressor and release all the pressure in the hose. This is critical for safety reasons, as the pressure in the hose can cause serious injury if released suddenly.
Once the pressure is released, you can locate the hole in the hose. Depending on the size of the hole and the material of the hose, there are a number of ways to repair it. For small holes, you can use tape or sealant to cover it up.
For larger holes, you may need to replace a section of the hose entirely. Whatever method you choose, make sure to test the hose thoroughly before using it again to ensure it’s safe and fully functional. With these simple steps, you’ll be back up and running in no time!
Unplug the air compressor from the power source
Unplugging the air compressor from its power source is a must-do step before proceeding with any maintenance or cleaning tasks. Once you turn off the compressor and release pressure via the pressure release valve, ensure that you unplug it from the outlet to avoid any accidents or electrical issues. It’s a crucial step that you should never overlook even if you’re in a hurry.
By unplugging the compressor, you’ll eliminate any potential hazards and make the task at hand a lot easier. Just imagine trying to clean or repair the compressor while it’s still connected to a power source? It’s like working with a ticking bomb, and one wrong move can cause an explosion. So, always put safety first and unplug the air compressor before doing anything.
Press the trigger to release any remaining pressure
If you’ve been using your air compressor for some time and need to turn it off for any reason, there’s one crucial step you should take before doing so, and that’s releasing the remaining pressure. By simply pressing the trigger, any air leftover in the compressor’s hose will be released, preventing it from building up and causing damage. This step is imperative for safety reasons as well since compressed air can pose a significant danger if released suddenly or unexpectedly.
Once you’ve taken this step, you can safely turn off your air compressor by switching off the power button and unplugging it. Remember to give it some time to cool down before storing it away. Keeping your compressor in good working order will ensure that it remains useful for years to come.
So, the next time you’re done using your air compressor and need to turn it off, make sure to press the trigger and release the pressure before switching the power button off.
Prepare the Hose for Repair
If you’re faced with a hole in your air compressor hose, don’t panic – you can fix it yourself with a little effort and some basic tools. The first step is to prepare the hose for repair. Begin by turning off the air compressor and unplugging it from the power source.
Next, locate the damaged section of the hose and clean the area thoroughly with soap and water. Once the hose is clean and dry, use a utility knife or sharp scissors to cut away any damaged or frayed parts of the hose. It’s important to create a clean, smooth cut so that the hose can be properly repaired.
If the hole is small, you may be able to use electrical tape to cover the area. However, for larger holes or more serious damage, you may need to use a hose repair kit or replace the entire hose. With a bit of care and attention, you can repair your air compressor hose and get back to work in no time!
Mark the location of the hole with a pen or tape
If you have a hole in your garden hose, don’t worry. It’s a common problem that can be fixed with ease. Before you begin, you need to mark the location of the hole with a pen or tape.
This will help you identify the spot and make the repair process much smoother. Once you’ve marked the area, you will need to prepare the hose for repair. To do this, cut out the area around the hole and discard it.
Once you’ve removed the damaged section, clean the area thoroughly with a sponge and water. Make sure the area is dry before proceeding with the repair. If the hole is big, you can insert a garden hose repair kit into the hole and twist it until it’s firmly in place.
Then, use a clamp to secure the repair kit to the hose. If the hole is small, you can use a hose mender to fix it. Simply slide the mender onto the hose and use pliers to tighten the screws until the mender is firmly in place.
With these simple steps, you can fix your garden hose and get back to enjoying your watering projects.
Clean and dry the area around the hole
Before you start fixing a hose, it is essential to prepare the area by cleaning and drying it to ensure a lasting repair. Begin by inspecting the damaged section of the hose and make sure you have all the tools you will need for the repair. Clean the area around the hole to remove any dirt or debris that could interfere with the repair process.
You can use a cloth or a mild detergent to clean the surface from any contaminants. Once the area is clean, dry it off completely to avoid any moisture contamination that can compromise the adhesive or the patch you use to repair the hose. Preparing the hose correctly will save you time and effort by ensuring a successful repair.
Therefore, take your time and make sure the area around the damaged section of the hose is free from dirt and moisture.
Patch the Hole in the Hose
If you’re working with an air compressor, you know how critical it is to have a good hose. Unfortunately, hoses can develop holes from time to time, and this can seriously compromise your performance. But don’t despair! There’s an easy fix for this problem.
First, you’ll need to locate the hole and mark it. Then, you’ll want to cut a piece of rubber that’s slightly larger than the hole. Apply some rubber cement to the patch and press it firmly onto the hose, making sure the edges are sealed tight.
Let it dry for at least a few hours – ideally overnight – before using the hose again. This should do the trick and get you back up and running with minimal downtime. Just remember to keep a spare patch and rubber cement handy, just in case it happens again!
Cut a rubber patch slightly larger than the hole
If you’ve noticed a hole in your hose, don’t worry! Patching it up is a simple task. The first step is to cut a rubber patch that’s slightly larger than the hole. You can find rubber patches at most hardware stores and they’re inexpensive.
Once you have your patch, clean and dry the area around the hole with a cloth. Then, apply a thin layer of rubber cement to the patch and the area around the hole. Carefully place the patch over the hole and press down firmly.
Make sure the patch is securely in place before using the hose again. By patching up the hole, you can save yourself money by avoiding the need to buy a new hose. With a little bit of effort, your hose will be as good as new again!
Apply rubber adhesive to the patch and the area around the hole
So your garden hose has a hole in it, and you’re wondering how to patch it up without having to buy a new one? Well, you’re in the right place! One thing you can do is apply rubber adhesive to the patch and the area around the hole. This will ensure that the patch sticks properly and won’t come off easily. Make sure to clean the area around the hole with a dry cloth before applying the adhesive.
Once you’ve applied the adhesive, wait for it to dry completely before using the hose again. It’s important to note that this method works best for small holes, so if the hole is too big, it might be time to replace the hose. Don’t let a small hole put a damper on your watering plans.
With a little bit of adhesive, your hose will be back in action in no time!
Press the patch onto the hole and hold it in place for several minutes
If you’re faced with a hole in your hose, there is a simple solution that can save you time and money – patching the hole. Don’t worry, it’s an easy process that you can do yourself in just a few steps. First, make sure your hose is dry and clean, as any dirt or moisture can interfere with the patch’s adherence.
Then, prepare your patch by cutting a piece of rubber or adhesive material that is slightly larger than the hole. Once you have your patch ready, apply some adhesive to the back of it, and place it over the hole on your hose, making sure to center it properly. Press the patch onto the hole firmly, and hold it in place for several minutes to ensure it sticks properly.
Once you have held it down long enough, carefully remove your hands and let the patch dry for a couple of hours. It’s important to keep in mind that patching a hole in your hose is not a permanent solution, and that you may need to replace the hose at some point in the future. However, if the hole is small and the damage isn’t too severe, patching it can prolong the life of your hose and save you from having to make a costly replacement right away.
So, don’t panic if you find that your hose has a hole in it. With just a few simple steps, you can patch it up and be back to watering your plants or washing your car in no time. Remember to keep your hose clean and dry, apply adhesive to the patch, and press down firmly for several minutes to ensure it sticks properly.
With these tips in mind, you’ll be a hose patching pro in no time!
Test the Hose
If your air compressor hose has a hole in it, don’t worry because you can fix this issue yourself. The first step is to locate the hole in the hose. Once you have found the hole, cut a small piece of rubber that’s slightly larger than the hole.
Using some rubber cement, apply it to both the hole and the piece of rubber. Place the piece of rubber over the hole and hold it in place for a few minutes until the cement dries. Once it has dried, test the hose by running air through it to make sure that there are no leaks.
If the hose is still leaking, you may want to consider replacing it altogether. Remember, when fixing a hole in an air compressor hose, safety should always be a top priority. With a little bit of patience and the right tools, you can fix the problem and get back to work in no time.
Wait for the adhesive to dry completely
When it comes to fixing a leaking hose, using an adhesive is a common solution. However, waiting for the adhesive to dry completely is crucial to ensuring a successful repair. You don’t want to find yourself back at square one because you didn’t give the adhesive enough time to bond properly.
To test the hose after the adhesive has dried, turn on the water and check for leaks. If you notice any leaks, turn off the water and reapply the adhesive. Remember to wait for the adhesive to dry completely again before testing it once more.
In some cases, the adhesive may not be enough to fix the leak and you may need to replace the hose entirely. This can be especially true for older hoses that have suffered significant wear and tear over the years. Don’t be afraid to invest in a high-quality hose that will last you for years to come.
Overall, taking the time to properly repair or replace your hose is important to keep your garden in top shape. Don’t rush through the process and make sure to follow the manufacturer’s instructions to ensure the best results. With a little patience and effort, your hose will be back in working order in no time.
Reconnect the hose to the compressor and turn it on
When it comes to testing the hose of your air compressor, it’s important to take a few steps to ensure everything is working properly. Start by reconnecting the hose to the compressor and turning it on. Check for any visible leaks or damage to the hose, and make sure it is properly connected to the compressor.
Once the hose is securely connected, turn on the air compressor and listen for any unusual noises or vibrations. As the compressor runs, check the pressure gauge to ensure it is maintaining the correct pressure. Finally, use the hose to blow out some air and check for any obstructions or blockages.
By following these simple steps, you can ensure that your hose is in good working condition and ready for use whenever you need it. Remember, regular maintenance is key to keeping your air compressor functioning at its best, so be sure to keep an eye on your equipment and address any issues as soon as they arise.
Check for any air leaks or pressure drops
When it comes to maintaining your pneumatic equipment, it’s important to check for any air leaks or pressure drops. One way to do this is by testing the hose. Start by inspecting the hose for any visible damage or wear.
Then, turn on the air pressure and listen for any hissing sounds that could indicate an air leak. You can also use a spray bottle filled with soapy water to check for leaks. Simply spray the hose and fittings and look for bubbles.
If there are bubbles, this indicates a leak that needs to be repaired. Additionally, check the hose’s pressure by using a pressure gauge. This will help you determine whether the hose is functioning properly or if it needs to be replaced.
By regularly testing your hose, you can ensure that your equipment is working at its best and avoid any potential safety hazards. Remember, prevention is always better than a cure!
Conclusion
Fixing a hole in an air compressor hose may seem like a daunting task, but with a little bit of elbow grease and the right tools, it is entirely possible to get your hose up and running like new again. Not only will you save money on replacement costs, but you will also have the satisfaction of knowing that you tackled the problem head-on. So go ahead, channel your inner handyman, and get to work fixing that hole – it’s time to get back to work!”
Fixing a hose can be a quick and easy project as long as you follow these steps.
Before attempting to fix a hose, it’s crucial to test it first to determine the severity of the issue. Testing the hose involves checking for any leaks, cracks, or bulges that might cause problems down the line. The easiest way to test the hose is by turning on the water.
If water leaks from the hose, then there is definitely something wrong with it, and it’s time to fix it. However, if there are no visible leaks, you can also inspect the hose manually to check for any signs of wear and tear. This will ensure that you spot any potentially dangerous problems that may require immediate attention.
Testing the hose is an essential step that ensures you find and fix problems before they cause significant damage or inconvenience. Remember that a quick fix now can save you from much larger headaches in the future.
FAQs
What causes holes in air compressor hoses?
Air compressor hoses can develop holes due to wear and tear, punctures, or exposure to heat and chemicals.
Can a hole in an air compressor hose be repaired?
Yes, a hole in an air compressor hose can be repaired using either a patch or a hose clamp.
What tools are needed to fix a hole in an air compressor hose?
Depending on the method of repair, tools such as a patch kit, hose clamp, scissors, and pliers may be needed.
Is it safe to use an air compressor with a hole in the hose?
No, it is not safe to use an air compressor with a hole in the hose as it can cause injury or damage to the equipment.
How can I prevent holes in my air compressor hose?
Regular inspection and maintenance of the hose, avoiding kinks and twists, and proper storage can help prevent holes in air compressor hoses.
Can I use duct tape or electrical tape to fix a hole in an air compressor hose?
No, duct tape or electrical tape is not recommended for fixing holes in air compressor hoses as they may not provide a secure and long-lasting repair.
How much does it cost to replace an air compressor hose?
The cost of replacing an air compressor hose varies depending on the type and length of hose needed, but it can range from $20 to $100 or more.